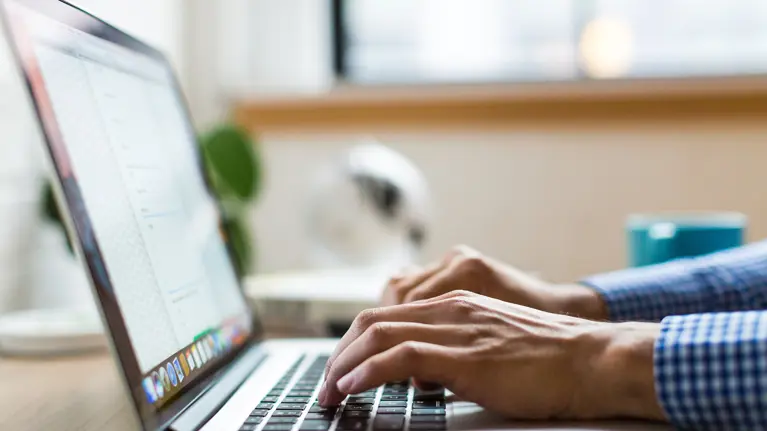
Artificial Intelligence needs history data – don’t delete it
Process data is the raw material that the machine learning algorithms need to create mathematic models that help operators, engineers and managers improve mill operation.
In their quest for autonomous mill operation for optimizing operations, cost and quality, the pulp and paper industry is looking at the possibilities of Artificial Intelligence. Key to making it work is collecting data in huge quantities – and keeping it stored to let AI work its magic.
Modern paper, board and pulp mills produce huge amounts of data. For example, there can easily be tens of thousands of data tags in their operational systems, measuring the properties of the product or the status of the machinery. The frequency of the measurements is typically seconds or even milliseconds, which leads to terabytes of data very soon.
In such an environment, it is a tempting idea to optimize OT/IT hardware capacity and delete the history data in the systems, or to aggregate the data in your data warehouse and similar solutions.
This is definitely not a good idea.
Consider the value of your data compared to hardware capacity cost. The value of your data is many times more than the hardware cost to store it. If you delete your history data, you might lose precious information about your process and operations.
Data is the food AI needs
As Yazzoom, TietoEVRY’s partner specializing in AI applications for the pulp and paper industry, says, it is important to retain process history data to boost AI capabilities.
Process data is the raw material that the machine learning algorithms need to create mathematic models that help operators, engineers and managers improve mill operation. These mathematical models are used to detect anomalies in the sensor or equipment functioning, to predict product quality with virtual sensors or to avoid unplanned stops by predicting upcoming machine failures. They also help process engineers identify how they can achieve certain process or product targets.
Equally important aspects are metadata, data quality and granularity. Metadata is important because the data scientist will collaborate with the local domain experts to understand which process data might be relevant to realize a specific data analytics objective.
The required data quality and granularity depends on the use case. If you want to be ready for any future use case it is better to use only lossless data compression like in TIPS Info, instead of using data historians with lossy data compression methods. For variables that need a higher sampling frequency than once per second, it is common practice to only store snapshots of the features in the long-term storage, rather than the raw signals themselves.
History helps make future changes
History data also helps cope with process changes and the introduction of new machinery, new devices and sensors. That information can be used as additional contextual information by the mathematical models or at least to help process engineers and data scientists understand the origin of changes in the process data. Significant process changes may be a good reason to delete old process data, but even then, the data could still be useful for certain objectives, for example, predictive maintenance of old equipment still used in the new process.
Where and how to keep the data?
TietoEVRY has a long partnership with MOPSsys, a company providing a state-of-the-art process historian database known as TIPS Info. The historical storage of time-based process data in combination with quality data and comments from operators is a gold mine for analysis tools such as AI. The value increases with the amount of data, the length of history, and the capability to explain the data with good descriptions.
The AI value is not the only value, though. TIPS Info includes numerous functions for ad hoc analysis and drilling down to root causes. This will give the production team faster feedback from data with more exact KPIs and better decision support to reduce waste and meet quality targets.
Retaining process data in systems is as important as maintaining the human know-how that operators have accumulated over the years. Just as the operator expertise comes from working at the mill for years, the AI model can learn the “normal” and “abnormal” conditions of the process by learning from past data. To achieve this, you need process data from a long-enough period and in enough detail.
TietoEVRY’s world-class mill execution system TIPS industry solutions and services has now AI capabilities included. The new concept is called “TIPS AI”.

With all his 35-year working life in the forest industry, from systems development to leading international service teams, Heikki has exceptional capabilities to capture business benefits for TietoEVRY’s customers through well performing IT.